Q: Why are those little copper tubes installed in the resistance spot welding electrode holders we purchase? They’re fragile and our spot welding machine operators often throw them away when they get bent.
A: Problems commonly observed during our company’s service calls at customers’ plants indicate that the proper use of water tubes in resistance welding electrodes is not well understood.
Although small and seemingly insignificant, those little tubes serve an important role in making good-quality resistance welds. Copper electrodes, although alloyed with chrome and other materials for added strength, must be kept as cool as possible because excessive heat allows the nose to soften and mushroom, leading to a significant drop in weld quality.
As the face of an electrode gradually mushrooms, the welding current is spread over a large and the current at any one point is decreased. Therefore, if the welding machine’s heat and weld time settings are not adjusted, or the tips are not dressed or replaced, welding quality degrades over time.
Water tubes serve an important role in making good-quality resistance welds.
However, a properly installed water tube forces cooling all the way to the bottom of the cavity drilled inside the tip and removes heat faster from the tip of the electrode. This reduces copper softening and helps maintain electrode contact diameter. In this way, weld quality and tip life are maximized.
Water tubes coming in two basic styles: sliding and spring loaded. An adjustable sliding tube with the end cut on a 45-degree angle is the most common type of water tube used in resistance welding applications. Its diameter is sized to fit in or on a stationary tube threaded inside the electrode holder.
As a new spot welding tip is installed, make sure to extend the sliding tube all the way out prior to seating the tip into the tip holder. By using this method, the sliding tube will self-adjust inside the tip as it is installed, ensuring that the tube reaches all the way to the bottom of the tip’s water cooling cavity.
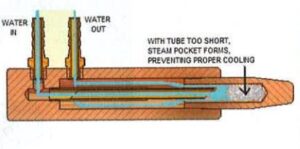
Fig. 1 – The water tube must reach to the bottom of the cavity or cooling water may not reach the tip.
The 45-deg angle cut on the end of the tube is designed to allow water to flow back out of the cavity after striking the hottest part of the tip first. If the water tube does not reach all the way to the bottom of the cavity, a steam pocket may form and cooling water may not reach the end of the tip where it is needed – Fig. 1. If the tube is not long enough, insert a proper one to match the electrode being used.
A spring-loaded water tube self-adjusts and seats automatically, but electrode holders with spring-loaded tubes are not well suited for use with offset tips equipped with sliding water tubes installed by the manufacturer.
Using water tubes properly will pay big dividends in weld quality and electrode life. Don’t throw them away!
Why Water Tubes Are Important
- Steel melts at about 2500°F and a typical spot weld is formed at about 2400°F at the interface of the two pieces of metal being welded.
- Electrodes made from copper alloy serve the dual purpose of conducting the high welding current to the weld area and applying forging force.
- Contact surfaces of electrodes can reach 1900°F during the welding process.
- Copper electrodes cannot withstand such high temperatures without deforming.
- Copper’s conductivity degrades and the weld face mushrooms as it heats up.
- Therefore, most resistance welding electrodes are water cooled, or should be.
- Small-diameter water tubes typically made of brass or copper force the flow of cooling water down inside an electrode’s internal cooling passage to the point closest to the weld.
- Weld quality and electrode life will degrade rapidly if water tubes are not used.
Things to Watch For
- Don’t discard water tubes!
- If tubes must be replaced, make sure the end is cut on a 45-deg angle to allow for proper water flow – Fig. 2.
- Water should be circulated as close as possible to the weld, so make sure the water tube reaches all the way down inside the tip.
- If the tube is not properly positioned, an internal steam pocket may form in the area closest to the weld and cooling water will not circulate all the way to the end of the water hole cavity.
- For improved cooling, use straight electrode tips when possible, rather than offsets.
- When using offset electrodes, select one that incorporates an internal water tube.
- If weld access is a problem, use offset tip holders and straight tips rather than offset tips in straight holders.
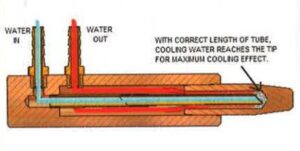
Fig. 2 – Cutting the end of a water tube at a 45-deg angle allows proper water flow.
Following are results from a research project conducted by Roger Hirsch of Unitrol Electronics titled “Influence of Water Temperature and Flow on Electrode Life.” The entire paper can be downloaded here.
Positioning the adjustable cooling tube 1″ back from the end of the inside water hole of the electrode had a major influence on tensile strength, weld nugget diameter, and electrode face diameter. Compared to a test run on a 0.050″ cold-rolled steel with a properly positioned sliding tube and operated at the same water flow and temperature, the mechanical change over the 8,000 weld run was as follows:
- Tensile strength decreased 27.6%
- Weld nugget diameter decreased by 18.2%
- Electrode face diameter increased by 42.0%