Spot Welding Safety
Spot welding safety is among one of the main priorities of T. J. Snow Company. While spot welding machines are widely used in sheet metal shop and are generally safe machines, several safety concerns should be considered. These safety concerns include:
- Pinch point hazards between the welding electrodes or tips
- Expulsion of sparks or pieces of molten metal
- Improperly grounded machines
- The creation of strong electromagnetic fields.
While spot welders are safe to use, there are several precautions operators should embrace.
Pinch Points
Depending on the material thicknesses being spot welded, a strong weld joint requires a forging pressure (pinch force) ranging from several hundred to several thousand pounds. And if the operator is careless, these pinch point forces will cause severe injuries to fingers and hands, including possible amputation.
An old-style foot-operated rocker arm spot welding machine is the safety type of spot welder ever designed. With a mechanical foot lever force delivery mechanism linked to the welder’s upper arm, the operator will quickly let up on the lever and release the pinch point if his finger happens to get caught between the electrodes.
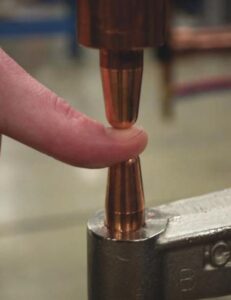
The “pinch point” between the welding tips can be potentially dangerous.
Although still available today, foot-operated spot welders have significant limitations because they cannot produce the high forging force required to produce strong and attractive welds in anything thicker than very light-gauge sheet metal. In addition, using a foot-operated welder to make multiple spot welds in quick succession is tiring. For these reasons, most rocker-arm and press-type spot welders sold today are air-operated and use a pneumatic cylinder to provide the required weld force to the electrodes.
Rocker-arm spot welders are preferred for most sheet metal shops due to their versatility. And like a loaded gun, all air-operated spot welders are dangerous if not operated with proper training and safety precautions. For example, a typical air-operated rocker arm spot weld set to deliver 600 pounds of weld force with a quarter-inch-diameter electrode weld face will deliver more than 12,000 pounds per square inch to the part being welded, and it will deliver that same force to the operator’s finger.
Adding to the potential danger is that most air-operated welding machines, which are typically initiated with an electric foot switch, will automatically complete, a full welding sequence regardless of what’s between the tips.
So, how can spot welder safety be enhanced?
- If not already present, install a graphic pinch-point warning sign on the machine.
- Train operators properly, including verbal and written instructions, regarding the importance of keeping their hands away from the moving electrodes.
- Make sure the foot switch used for machine initiation has a top and side shroud installed to prevent accidental activation.
- Require anyone who works in or travels through the spot welding department to wear safety glasses with side shields at all times.
- If possible, have the operator hold the parts being welded with both hands while the assembly is manipulated in the throat of the machine to access all weld locations.
- Prior to welding, adjust the open gap between the electrodes to the minimum space required to load the part being welded. If possible, this gap should be about a quarter inch. The goal is to make it impossible to place a finger between the tips before the weld stroke takes place.
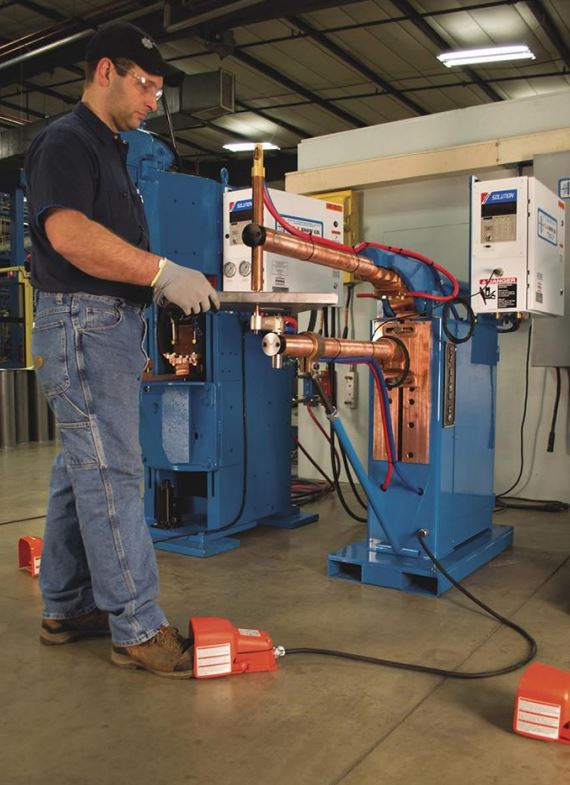
A standard air-operated rocker arm spot welder is very safe to use, but operators should still take precautions.
To overcome clearance problems caused by such a short working stroke, a retractable-stroke air cylinder is a highly recommended option when ordering a spot welder. Typically initiated with a separate foot switch, the retraction feature, sometimes called “high lift,” makes it easier to load three-dimensional parts, such as those with flanges, into the throat before welding.
Retraction raises the upper electrode to allow the extra clearance needed to load the part into the machine’s throat before reverting to the short working stroke for repetitive welding.
However, if the operator has not been trained to use this retraction feature, or if it is not adjusted properly, an additional pinch-point hazard can arise when the machine comes out of retraction and closes the gap between the tips before welding.
Occupational Safety and Health Administration inspectors sometimes treat spot welders like a press and require passive guarding against pinch-point injury. In this case, there must not be a way to defeat the passive system and overall machine safety cannot depend upon adjustments by the operator.
At present, the best way to address this requirement is by adding a “soft touch” pinch-point safety enhancement to the welder’s control. This electronic device, which can be added to most existing welder controls, brings the electrode tips together with low force and then checks for electrical conductivity through the parts being welded. If the soft-touch circuit fails to sense electrical conductivity, it does not allow the machine to apply the full forging force required to make the weld. In other words, it must detect metal between the copper tips rather than a finger. If conductivity is not sensed, the weld sequence is interrupted and the electrode lifts and releases the pinch point before serious injury can occur.
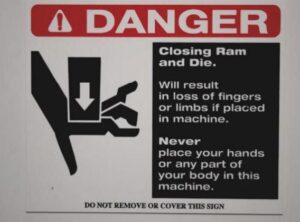
A warning sign similar to this should be on every spot welder.
Some other safety considerations when operating spot welders:
Weld Expulsion
Expulsion from the spot welding process can be dangerous because the shower of sparks represents pieces of molten metal flying out from the joint. In addition to potentially causing eye and skin injuries, weak and inconsistent welds can result.
Many sheet metal shops assume that expulsion is a normal part of the spot-welding process, especially when welding galvanized material. Often they just issue safety glasses, leather aprons, full face shields and arm sleeves. However, by using the right spot welding machine and having it set and operated properly, sparks will be greatly reduced or perhaps even eliminated.
Rather than guessing at the required settings, refer to the published weld schedule charts for various metal thicknesses that are available from several sources, including the Resistance Welding Manufacturing Alliance. A hand-held weld force gauge and a specialized secondary amperage meter make setting the variables of a spot welder much easier.
The pulsation feature of a spot welder control can also be used to reduce sparks, especially when welding thick material. Programming several impulses of relatively low heat with a few cool cycles between each pulse can avoid sparks and achieve a strong joint. Pulsation can also help when expulsion is caused by welding too close to the edge of the part.
Grounding
Spot welders convert incoming line voltage and amperage into low secondary voltage and high welding amperage at the electrodes. Since the secondary voltage is typically less than 10 volts, there’s usually no shock danger to the operator from touching the copper arms during the welding process. However, because welding transformers can fail, an improperly grounded welding machine can pose a serious danger to the operator. Be sure one side of the welder’s secondary circuit is properly grounded.
Grounding is also critically important when welding with a hand-moved portable spot welding gun that has a built-in transformer. This type of portable spot welder should not be used unless it is equipped with a ground fault device and a ground confirmation system to protect the operator. Without these safety devices installed in this type of welder, failure of the transformer could cause line voltage to pass through the operator to ground.
Electromagnetic Fields
A very strong electromagnetic field is created between the arms of a spot welder when the current flows while making welds. Due to the potential for exposure to EMF in the throat of the machine, a spot welder should not be operated by someone with an implanted medical device, such as a heart pacemaker or defibrillator.
This article was originally published in SNIPS Magazine, Vol. 86, No. 12 (December 2017)